Frequently Asked Questions
- Will a structural engineer stamp the drawings?
- Can you provide a 3-source electrical solution (standard, UPS, and generator)?
- Will all the drawings we receive be in a Revit format?
- What are the advantages to lessees of your system?
- How long does it take for installation?
- What about energy conservation?
- How will technical support in the US market be assured?
- What infrastructure components are not included in your integrated package?
- Can your system be removed and reinstalled at another location?
- Do any building services need to be shut down during installation?
- When was the technology developed and where do the rights reside?
- How are all the controllers, UBOX, fume hood controls, lab controls, and sensors coordinated into one system?
- What is the organizational flow of responsibility for the US market?
- Are your components UL certified?
- How much of the content is manufactured in the US?
- What is the major difference between your HVAC solution and that of standard MEP?
- What is the typical lead time for shipping the completed integrated solution?
- How easy is it to move a column or a fume hood?
- How is the design effort for the media ceiling integrated into the overall design process?
- Can your system be easily adapted to office, BSL1, BSL2?
- Can you provide a capability to allow for equipment taller than the general lab space ceiling height?
- Does any of your integrated software comprising your digitized solution have any obstacles when computing with other manufacturer's software or any BMS?
- Is your prefabricated solution assembled on site?
- What are the benefits of your solution over standard MEP?
Yes, as part of the drawing submission, they will be stamped by a structural engineer.
Yes, our busway and raceway components can be designed to provide electrical service no matter the source. We would like to work with the building electrical designers to ensure that we have the most efficient and cost-effective solution meeting the end user's needs.
We can provide high-detail PDFs and Revit 3D files of all the individual providers/service contractors, a list of materials needed, and the coordination plans that detail the interfaces between different suppliers the building, and so on. The drawings are to scale so additional measurements can be taken directly from them. Furthermore, we can work with an integrated BIM workflow from planning to execution and after-sales.
New lessees can reconfigure the space with minimal expense and focus capital on researchers. Our solution can be reconfigured at minimal expense in hours and/or days. Immediate activity can begin with little effort.
We will come in at least one week before installation to install the ceiling anchors.The space should be completely finished prior to installation so that no dust is created post installation. The entire prefabricated solution is assembled at waist height and then lifted to the ceiling anchors. A team of 5 can install 5,000 sq. ft. in a week. Multiple teams will be used for larger projects. There is no need to shut down any building services during installtion and each floor can be operational before moving on to the next level.
Due to thermal layering and the fact that above each light channel there is a vav contolled exhaust outlet, we can save up to 30% of energy consumption with this feature. Further, there is significantly less static pressure in our solution that when combined with coordination with the building system design could save not only additional enegy consumption, but also reduced building HVAC equipment. The third area of energy reduction is that all heating/cooling/recirculation of air intake, takes place precisely at the air inlet.
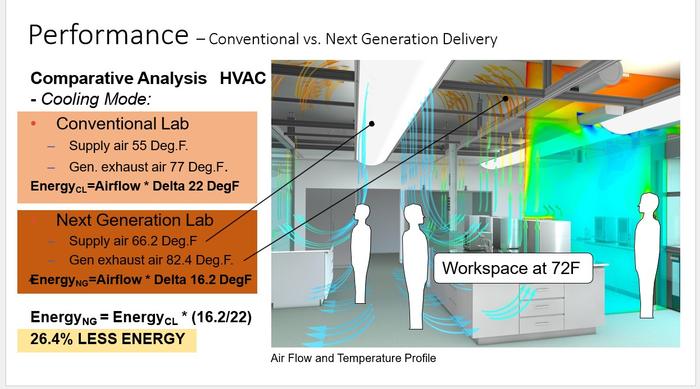
New England Lab as contractor for installation will have primary responsibility for any service and maintenance. C7-GLOBAL will maintain critical inventory of components and will continue to source more components in the US. A large portion of all the HVAC solution is already sourced in the US along with all the electrical, data, control, and sensors.
We do not provide a fire protection (sprinkler) solution. We will provide a local contractor with 3-D drawings and a suggested solution. We ask that the main air intake and exhaust ducts be installed by the building subcontractor. We suggest that sinks be placed along walls so that drainage does not impact future flexibility.
Yes. It can be uninstalled by hand as simply as it was installed. There may be some minor waste and replacement parts necessary, but you should be able to save up to 80% of the initial material costs.
No. All building services can be operable during installation. There may be a temporary interuption when local contractors make their connections of the building services to our installation.
The technology was developed and patented by H. Luedi + Co. AG over 20 years ago. C7-GLOBAL has exclusive rights to North America.
In our completely integrated and digitized infrastructure, all of these components are driven by Siemens software and analytics. This software is in BACnet protocol and can therefore seemlessly speak with any BMS which in North anerica would also be in BACnet protocol.
New England Lab (NEL) will make all drawing submissions and be the contracting party with the General Contractor. C7-GLOBAL and H. Luedi will provide all the technical support and engineering/design packages to NEL. All component suppliers will provide technical assistance at installation.
Yes. All major components are UL certified.
All the electrical components; busway, busway connectors, busplugs, raceway, column electrical module, and data cable trays are produced in the US. Almost all of the HVAC solution, with the exclusion of the HL-X-UBOX are produced in the US. Certain plumbing services are also US sourced. As we receive new projects, more of the content will be sourced in the US.
Each light channel is a pressurized air intake diffuser tube that creates a special air flow pattern in each aisle at very low air velocity. The air intake is distributed throughout the entire length of the light channel and creates an airflow pattern that allows for fume hoods to be moved to anywhere within the space. It also allows for partitions to be placed to separate labs and easily modify air flow requirements on control panels. Heating and cooling occur at the point of air intake in each aisle thereby minimizing energy consumption and creating climate control within each aisle.
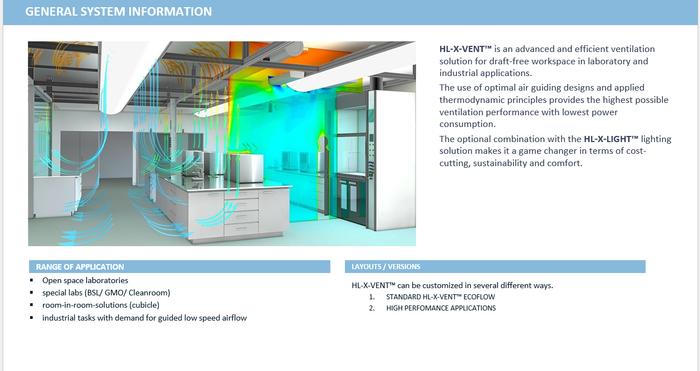
After acceptance of the drawings, the entire solution can be produced, packaged, and shipped in 6 months. Allowing for intial design discussions, shipping time, and installation, most projects can be completed in 9 months. Larger projects will require multiple installation teams.
Gas, coolant, water, and vacuum service connecting blocks are placed throughout the media ceiling allowing for easy connection to those services from any point. Columns typically weigh about 45-50 lbs. and can be easily disconnected from the quick connect, self closing connecting blocks and easily moved. There are 4 bolts at the top of the column connecting it to the grid. Disconnect the services, disconnect the bolts, lift the column and move it to wherever you require it. Quickly reconnect the services to the new connecting block and plug in to the busway. We prepare spare exhaust duct work in the media ceiling that can be moved to any aisle in which you decide to move a fume hood. All gases and electricity can be accessed from any position within the lab. The patented air flow pattern allows for this flexibility.
This is a design assist delivery method where H. Luedi + Co. will work with the design team very early in the project.
Yes. Since each aisle is its own air flow and climate controlled environment, partitions can easily be added and removed to modify the space for required use. Airflow rates and pressures can be modified on a control panel. Moving from BSL1 and BSL2 to office is as easy as removing the columns and adjusting the airflow exchange rate on your control panel. Moving from office to BSL1 and/or BSL2 will require adding media services to the light channel and hanging new columns. Not difficult at all and very easy access for the changes.
Yes, this is a common ocurrence in laboratory design. There are several work-around techniques that can be used. In these instances, all services are normally received directly from the media above. This is easily solved with discussions with the architects and lab planners.
Building Management Systems today, in North America, communicate using the BACnet protocol. Every single air valve, fan coil and lab room controller, that we source from Siemens, already comes with the ability to communicate using BACnet, natively.
When the contractor’s customer goes to his BMS, he can look at a graphic of a lab room and see the temperature and temperature set point, the supply air flow and the supply air flow set point and many more points. Those points in the world of BACnet are called “objects”. Our Siemens lab controls have the same “objects”. We can literally connect our objects to their graphics and the owner will not be able to tell if he is looking at a point from our Siemens technology or a point from any other manufacturer.
Yes, the entire set of all components is manufactured, package, and shipped to the site where it is assembled. The system is assembled at waist height and raised to the ceiling anchors. No building systems need to be shut down during installation. The space should be completely finished prior to installation so that no dust is created post installation.
• PROJECT FLOW… Up to 50% shorter project run time, due to modular, user-independent, structurized and parametrized 3D-Design + coordinated fast installation.
• SAFETY………………. Up to 30% reduced exposure to airborne particles or fumes.
• EFFICIENCY………… Up to 30% higher thermal efficiency compared to standard MEP. Up to 30% lower makeup air pressure and energy cost reduction.
• SUSTAINABILITY… Up to 30% reduced energy consumption and CO2 production especially for lab use designed hardware and control software.
• COMFORT ………….. Draft-free environment, climate on demand +-1°@ 15W/sf. Biodynamic LED- Light 0.75W/sf @ 55fc, high level noise attenuation.
• FLEXIBILITY……….. maximum flexibility with room in room solutions, adapts to all types of user requirements at any time with the HL-X-COLUMNS.
• AGILITY……………… fast reconfiguration and update of existing labs, no distruction, no dust or waste, minimal downtime paired with lowest renovation costs.
• TCO…………………… efficiency + flexibility + agility = lowest running costs = best TCO.